... we're working on creating holistic solutions for the working environments of tomorrow. To achieve this, we're collaborating with partners in more than 74 countries worldwide. We're helping organisations and people to shape the future successfully and sustainably with our services, products and commitment.
Sedus: a history of tradition and innovation
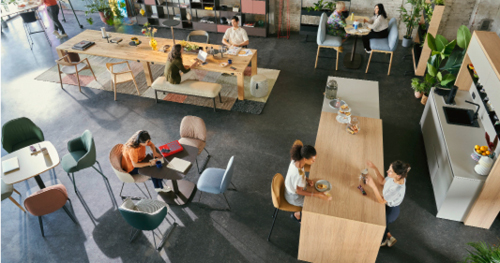
Today
2024
The Sedus Smart Café concept transformed the office into a social place for networking and collaboration. You might say that Sedus returned to its roots with the se:café wooden chair made from solid wood.
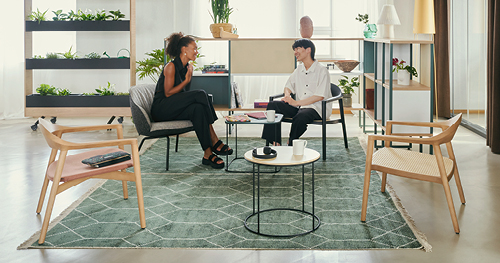
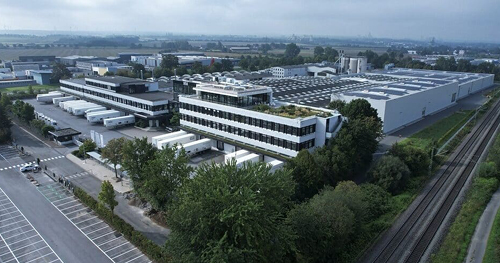
2023
After around two years of planning and construction, Sedus commenced operations at the new "Futura 2" production facility at the Geseke site.
2020
The Covid-19 pandemic accelerated the establishment of the home office. Sedus developed products that are optimised for the workspace within the user's own four walls. Product innovation highlights included the se:lab furniture system and temptation speed, the world's fastest motorised desk with a height adjustment speed of 150 mm per second.
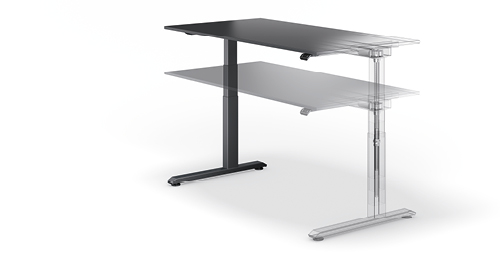
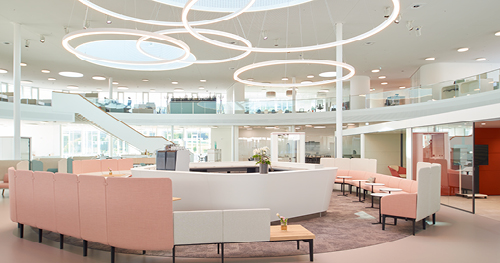
2018
The company headquarters was relocated to Dogern. The road link was renamed "Christof-Stoll-Strasse" in connection with this move. Spring 2019 saw employees move into the newly built "Sedus Smart Office".
2016
Sedus unveiled a world premiere; thanks to a newly developed digital space management system called se:connects, employees can use their smartphone or tablet to quickly book an available workstation or find their colleagues in the office building. This innovative technology provides facility managers with valuable data on office occupancy, which they can use for more efficient space utilisation and design.
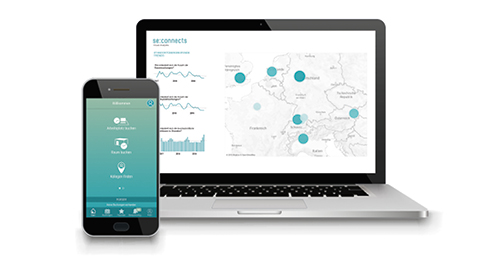
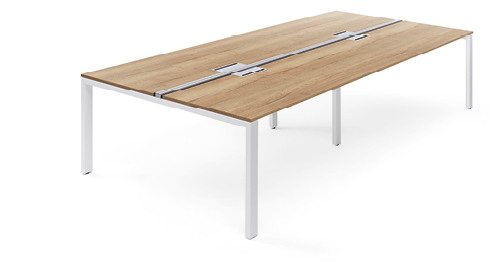
2014
The goal of bringing people together in offices and encouraging communication was a priority for Sedus in new product development. Non-territorial workspace design was becoming increasingly important with the new get together table system.
2012
Laser edging technology was introduced; an improved method of production for all furniture and table tops that creates a seamless, environmentally-friendly design edge.
Sedus was awarded the Environmental Prize for Companies in Baden-Württemberg.
With the aim of improving how people sit in the office, Sedus collaborated with the Technical University of Munich to develop a new kinematic seat concept for the swing up swivel chair. The result was healthier sitting through greater mobility. The chair adapts itself to people and not the other way round.
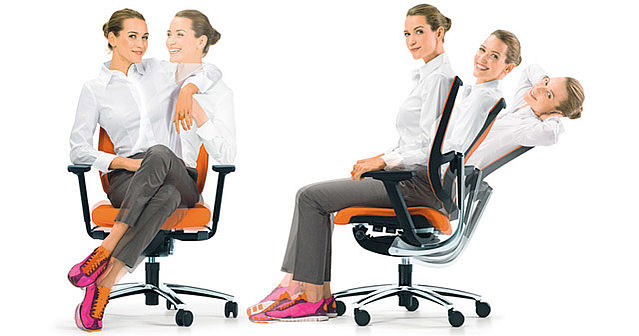
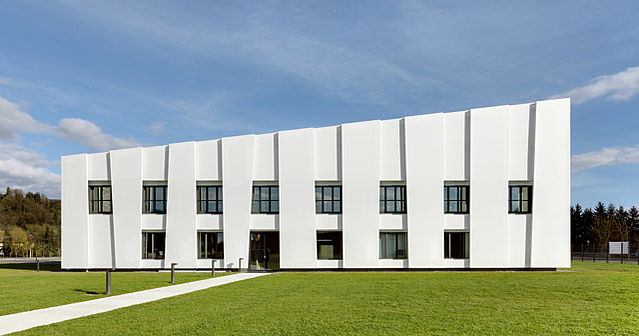
2010
The new Development & Innovation Centre in Dogern was completed.
Sedus was the first office manufacturer in the world to receive EMAS III certification.
2008
Gesika Büromöbelwerk GmbH changed its name to Sedus Systems GmbH, Geseke.
The "Similar-Plus" mechanism, with its pre-selectable opening angle and quick backrest pressure adjustment options, was developed.
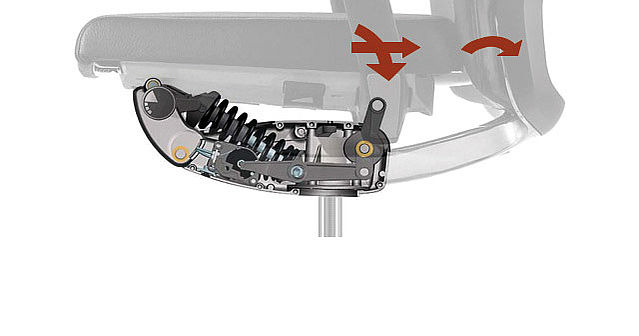
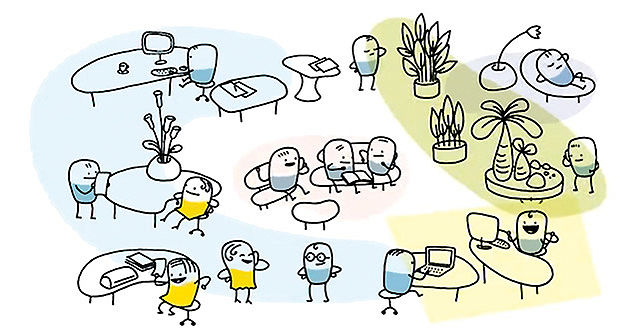
2005
The holistic furnishing concept, "Place 2.5 – the new emotional culture of the office," was developed. With this approach, Sedus became a trailblazer in its mission to design the office living environment as a place for people to feel good, and for well-being, in terms of company productivity.
2002
As a result of the merger with Gesika Büromöbelwerke GmbH, Sedus became a full-service provider of holistic office furnishings.
The Karl Bröcker Foundation founded in 1999 and based in Lippstadt, became Sedus' second main shareholder.
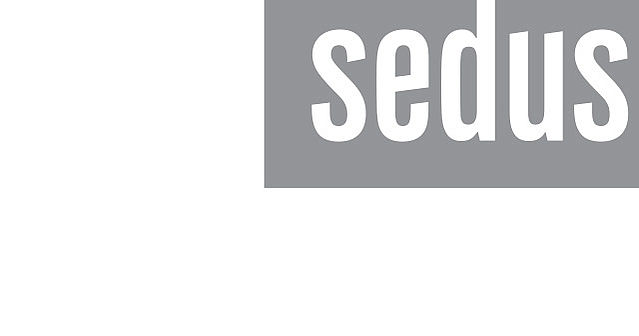
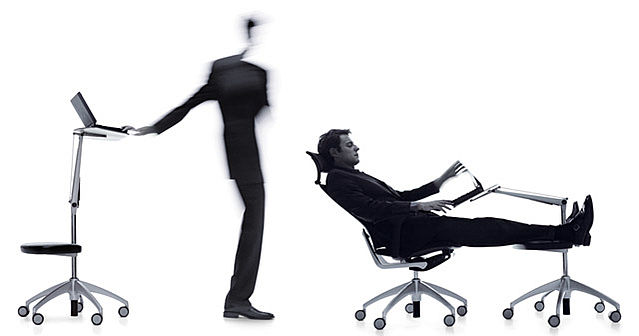
2000
Sedus open up was the first swivel chair with an opening angle greater than 40°. The company demonstrated its pioneering spirit with the slogans "Sleeping in the officeˮ and "Power nappingˮ. This emphasised the importance of regular posture changes, crucial for improving well-being in daily office work.
1999
Sedus Stoll AG acquired the majority shareholding in office furniture manufacturer Klöber GmbH, in Überlingen.
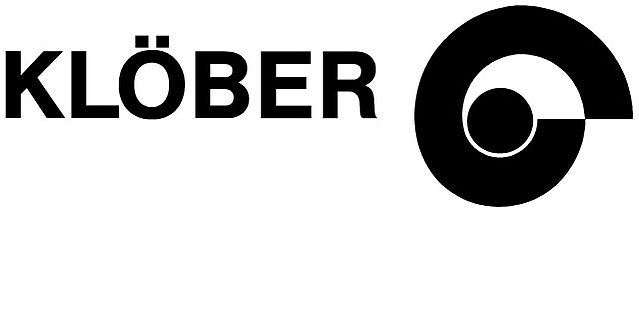
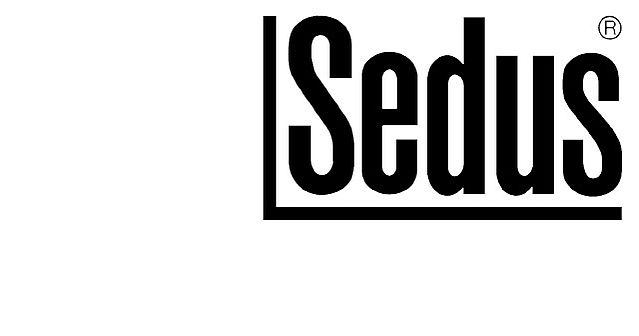
1995
The company was reincorporated as Sedus Stoll Aktiengesellschaft.
At this stage, the company was the first furniture manufacturer in Germany to undergo the eco-audit according to EU standards.
1994
The company's quality management system was certified in accordance with DIN ISO 9001.
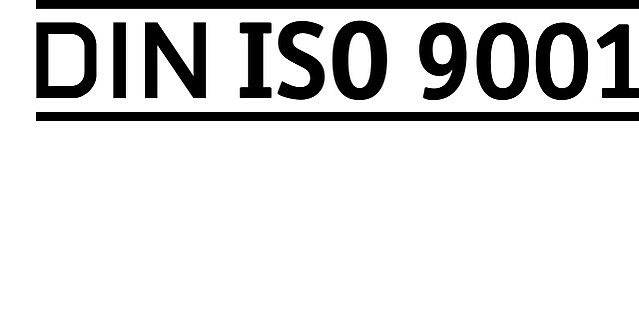
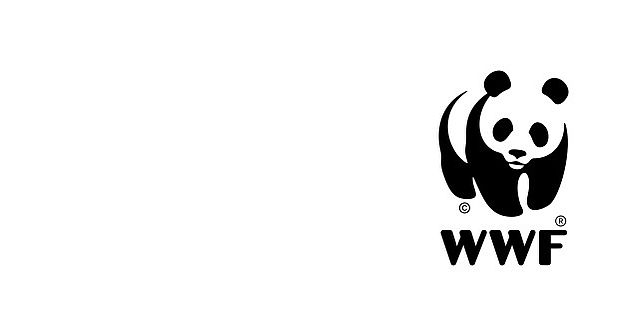
1993
Christof Stoll was voted Eco Manager of the Year by the WWF (World Wide Fund For Nature) and "Capital" magazine.
1985
Christof Stoll and his wife Emma established the non-profit Stoll VITA Foundation. They transferred their assets, which also included the majority shareholding in the family company operating as Sedus Stoll AG from 1995 onwards, to this foundation.
Due to his accomplishments as an entrepreneur, Christof Stoll received the Federal Cross of Merit in 1986.
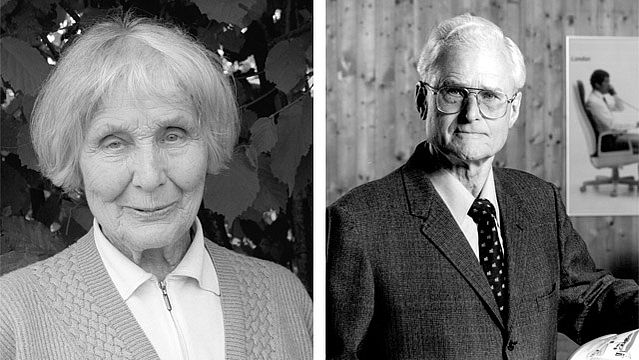
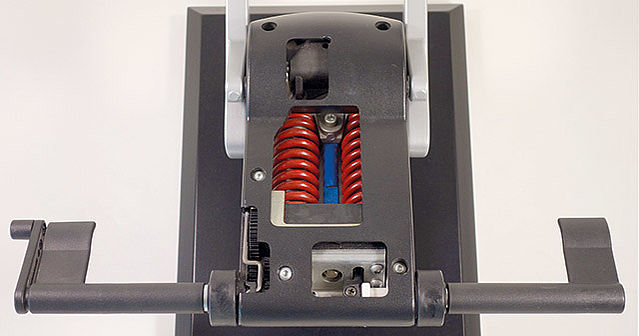
1973
The Anatomic chair, the Permanent Contact backrest and the "Similar" mechanism(principle of dynamic sitting)were developed. These innovations offered technical solutions to ensure optimum ergonomic support for people at work.
1970
As a consequence of the companies' growth, production was gradually moved over a period of several years to the new site in Dogern.This began as early as 1969. In 1970 Christof Stoll set up a separate development and testing department with the largest and most modern test laboratory in the industry, and hired Theo Hartmann, the first formally qualified designer. By 1987, a total of eight sales companies had been established in Europe.
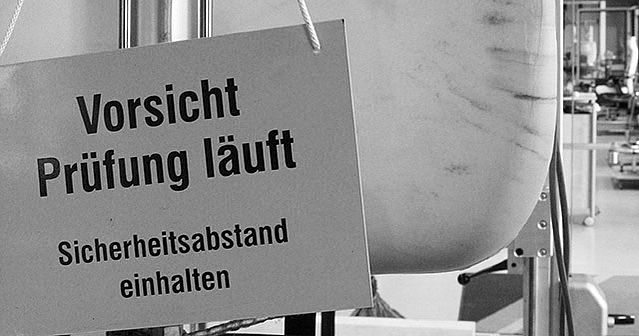
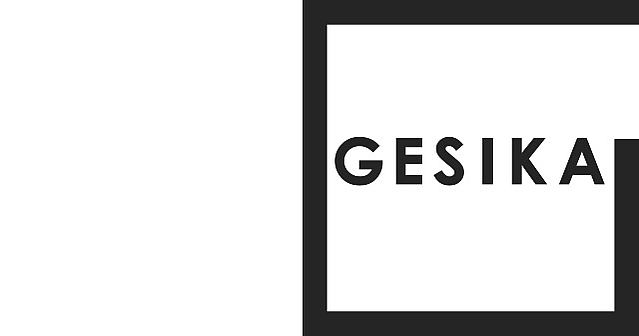
1962
Karl Bröcker established the company, Gesika Büromöbelwerke GmbH, in Geseke.
1953
Christof Stoll introduced profit participation for his employees.
In 1958, Christof and Martin Stoll split up the family enterprise, Albert Stoll OHG, and created two new companies: Christof Stoll KG in Waldshut and the Federdreh chair factory, run by Martin Stoll, in Tiengen.
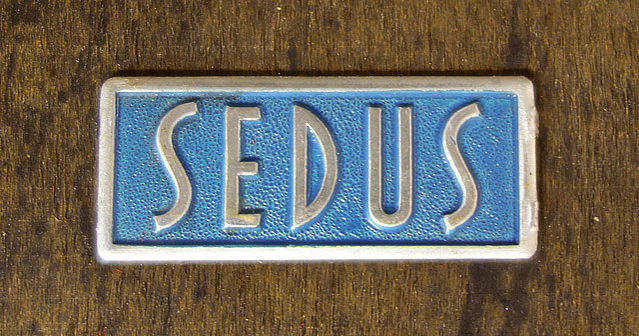
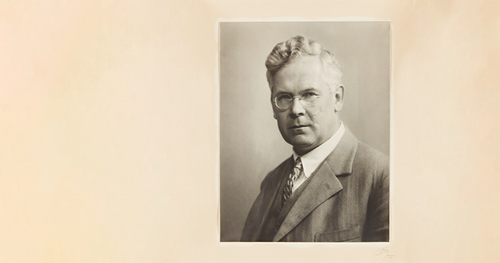
1937
Albert Stoll II died unexpectedly at the age of 54. Three of his four sons continued to run the chair factory: Albert Stoll III managed the factory in Koblenz, while Christof and Martin Stoll ran the Waldshut company together.
1929
The first swivel chair fitted with swivel castors was developed.
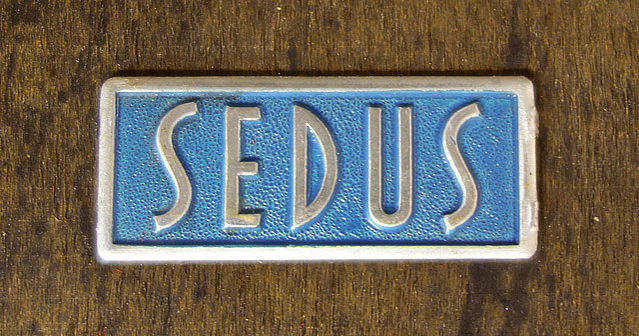
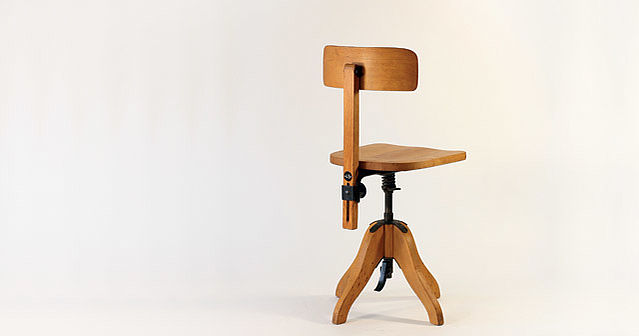
1926
Albert Stoll II improved the American office chair and eventually designed a swivel chair. He introduced his innovation to the public for the first time at the Leipzig Trade Fair. Itwas the internationally patented "Federdreh", the first swivel chair with a swivelling column suspension.
1912
Albert Stoll II started manufacturing spoke-back chairs in Waldshut. These models were strikingly different from the bent wood chairs and consisted of just a few curved parts. Horizontal and vertical rungs gave the Record Chair its stability and helped to support the backrest. Its individual parts were made on special machines that Albert Stoll II purchased in the USA. This eliminated the need for a significant amount of time-consuming manual work.
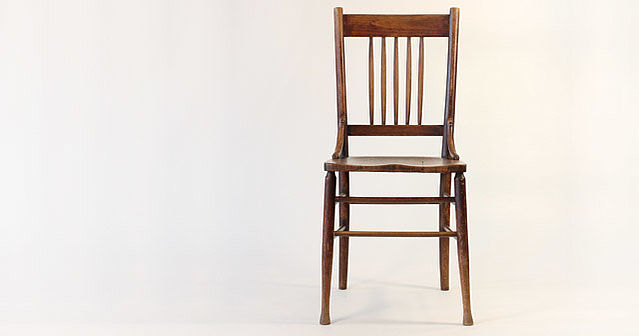
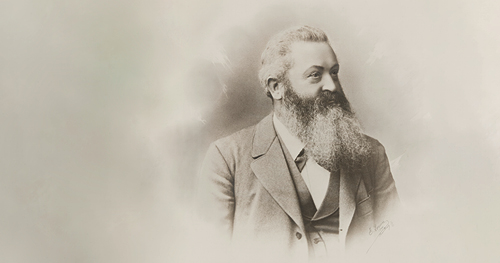
1897
Albert Stoll I died at the age of 61, leaving behind his wife Bertha, three daughters and a 15-year-old son, Albert Stoll II. Bertha Stoll continued to run the company and proved to be a successful businesswoman, which earned her the nickname "Sesselmacherin", or "chair maker". Meanwhile, Albert Stoll II completed his schoolingin Waldshut and studied mechanical engineering in Karlsruhe. In 1910, he went to the USA to continue his studies.
1890
Albert Stoll I developed the four-legged bent wood chair, which has a turned column with threaded insert to allow for height and swivel adjustment.
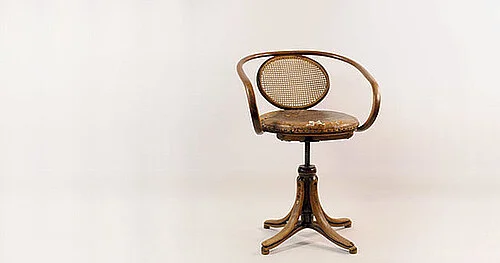
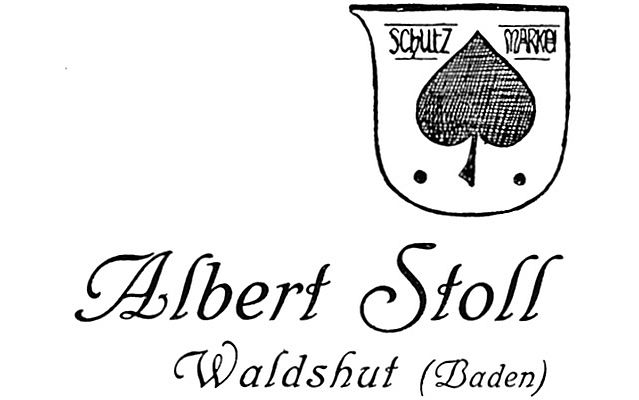
1871
Albert Stoll I, together with Max Klock, set up the “Stoll & Klock” chair factory in Waldshut. Following Klock’s departure in 1879, the company changed its name to “Albert Stoll”. Two to three dozen employees worked in this factory, making chairs out of bent wood. The most important raw material, beech, grew very close by, and there were plenty of workers living in this barely industrialised region – as well as home-workers to make wickerwork chairs. Waldshut's connection to the railway network created the ideal conditions for the distribution of products, in a time before the existence of fast, efficient and affordable transport by road.